Diagnosis and Solutions

We develop innovative, sustainable solutions to answer our client's most complicated challenges.
Start your journey with Elevate

01
Meet Our Experts
In our first meeting with you, we will present to you the benefits of continuously improving and how this will have a direct impact in increasing your operational revenue using the Toyota Production System mindset. This is how Toyota has set the high levels of maintaining operational success resulting in increased revenue.

02
Site Facilities Diagnosis
Factory diagnosis is conducted by our experienced consultant to actually visit the factory, grasp what points are important for improvement activities together with the customer, and explain how to proceed to gain agreement with the factory side.Our consultant with a wealth of experience and achievements conducts the factory diagnosis, identifies issues that customer could not see or notice, using our own radar chart, and recommend an ideal situation the customer should be. Please utilize our factory diagnosis to identify problems, create a foundation for a continuous improvement, or a first step in introducing consulting.

03
Gemba Consulting
Discuss diagnosis findings. Concerns of factory shop floor vary depending on the each environment. We have our wide range of experience and know-how and solve all issues, from quality, productivity, and delivery time issues to production line and flow reviews, measures to increase employee motivation, system improvements and information utilization, and overseas expansion.
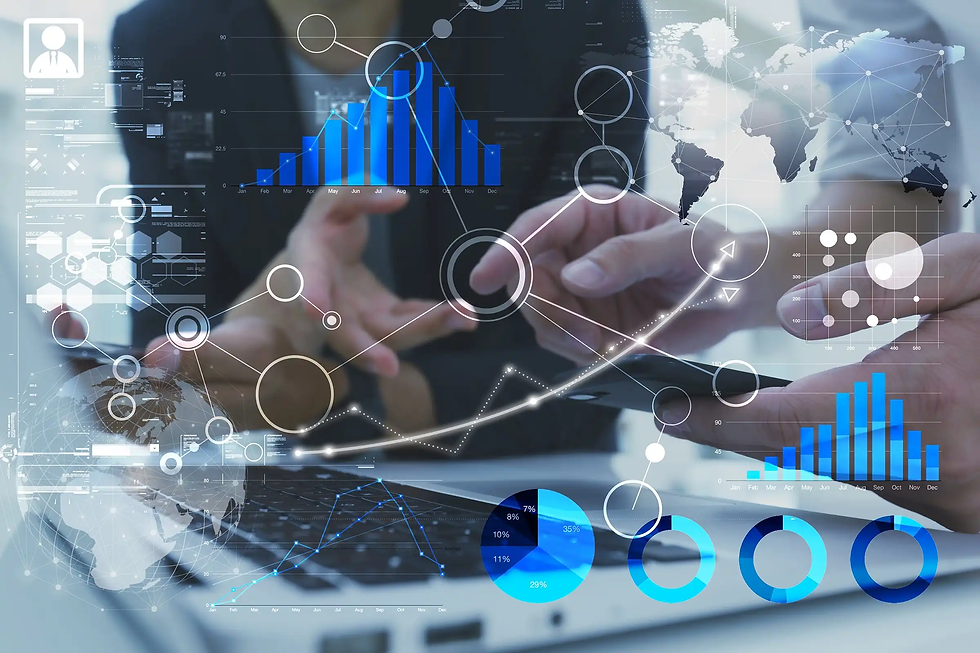
04
Remote Gemba Consulting
Remote Gemba Kaizen (shop floor improvement) service is a service that an experienced shop floor improvement consultant remotely diagnoses and improves the manufacturing shop floor using internet communication.For example, managers and operators wear cameras, earphones, and microphones, and its video and audio data is sent to the consultant in Japan, and the consultant gives instructions for work improvement etc. directly through the internet communication.
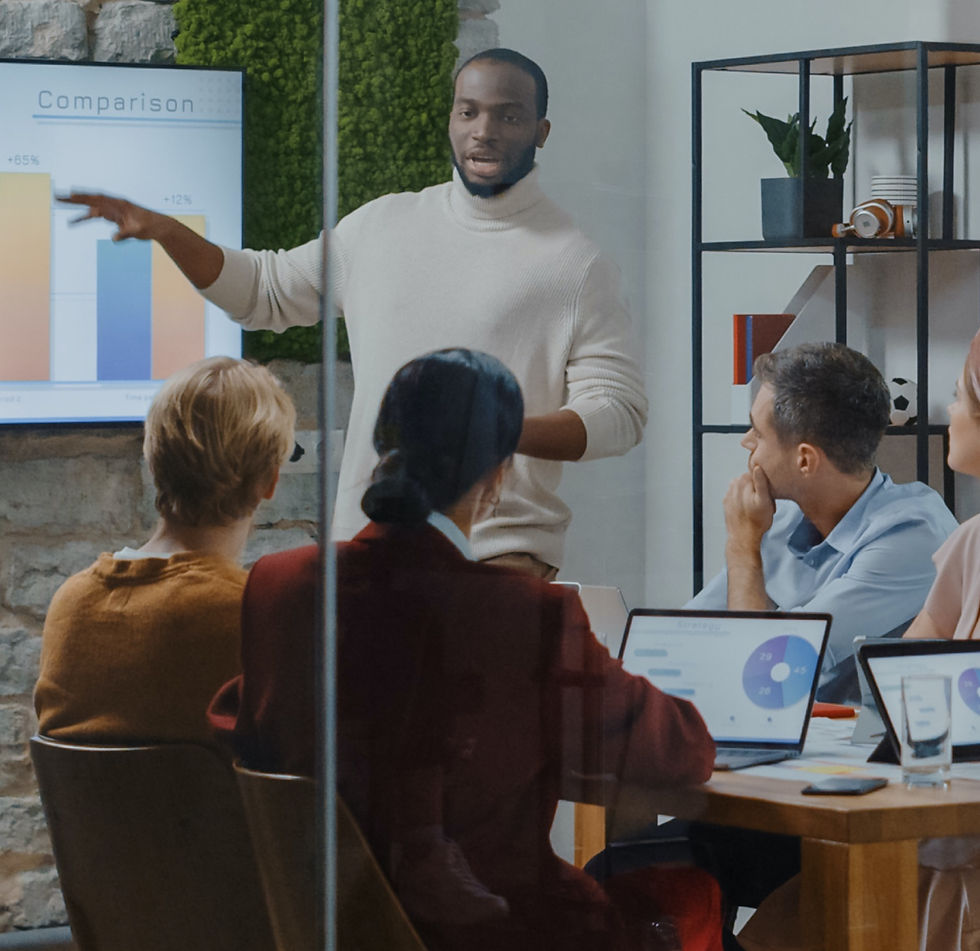
05
Basic Kaizen Training & Certification
The changing of the mindset to implement continuously improving. This training will take you to our 'dojo' Factory Training Center. This is where practical training will be imparted to all employees.
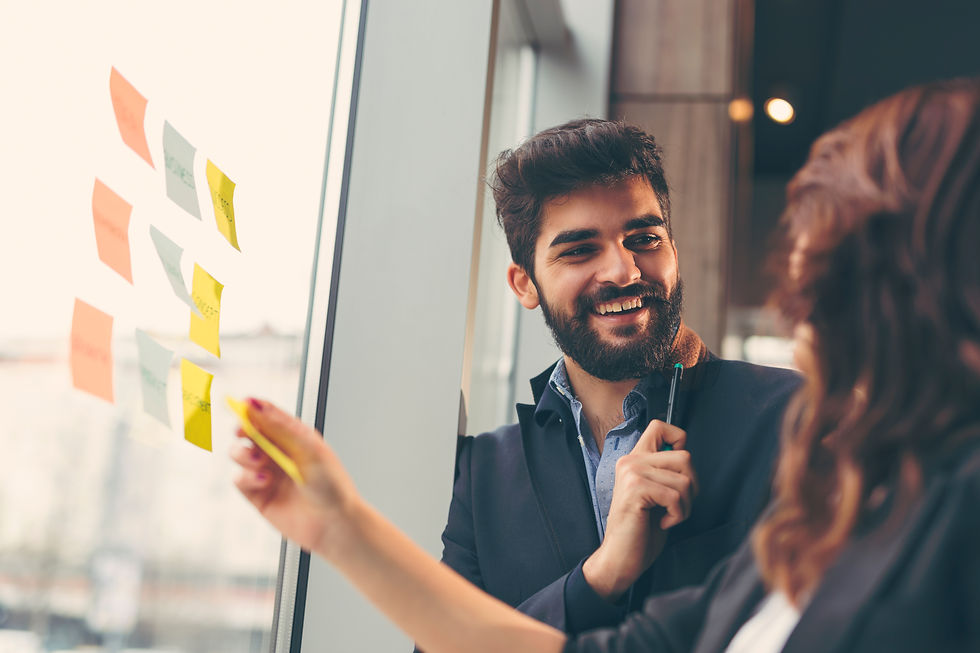
06
Seminar and Customised Training and Certification
6.1. 5S
6.2. Daily Management
6.3 Visualisation
6.4. Human Resource Development
6.5. Improvement
6.7. Logistics
6.8. Quality
6.9. TPS Dojo
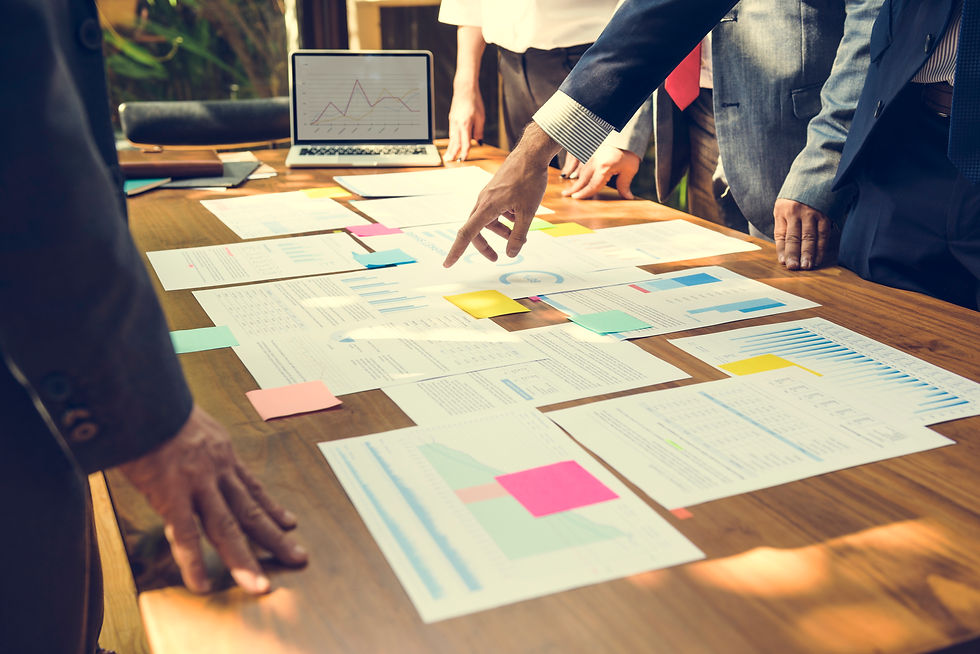
07
Annual Monitoring Plans
7.1. 6 Months Plan
7.2. 12 Months Plan
7.3. 18 Months Plan
7.4. 24 Months Plan
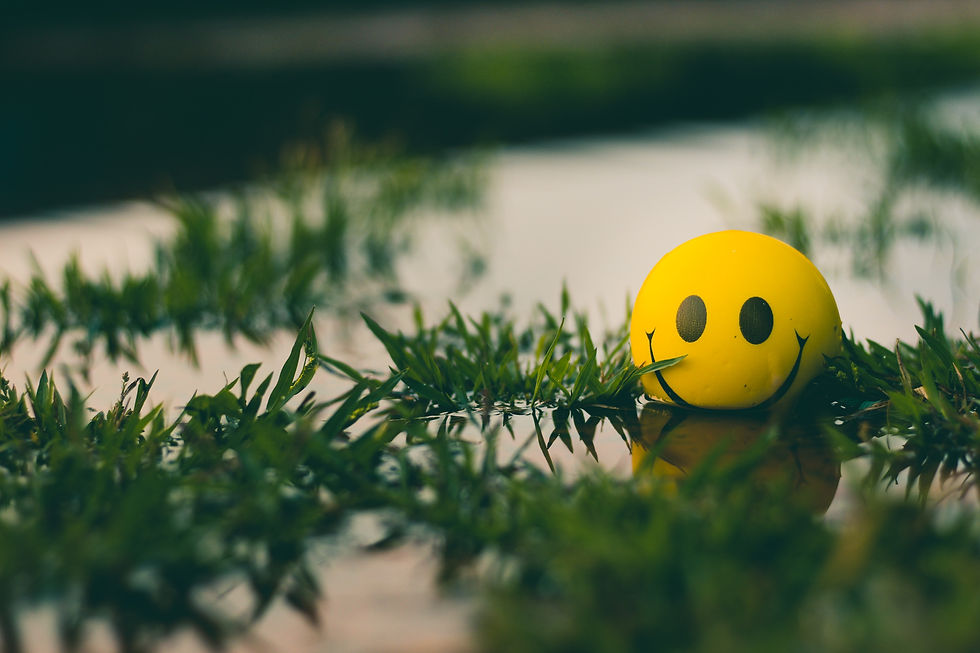
08
Feedback
We want to hear from you.
Different levels of diagnosis?
01
The Scoping
-
Definition of the area to be improved
-
Level of alignment of managers
-
Identification of strengths and weaknesses
02
The Excellence Benchmark
-
Internal repository of good practices
-
External benchmark / ELEVATE benchmark
-
Measurement of deviations from the benchmark
03
Progress Monitoring
-
Measurements of the application of good practices
-
Successive and comparable measurements over time
-
Comparison of progress by area or team
04
Multiple Evaluations
-
Each participant can make several evaluations
-
Allows to evaluate a priori non predefined 'subjects'
-
For example, evaluation of all projects in the organization
05
The Analysis
-
Detailed analysis of an area
-
Quantitative and qualitative evaluation
-
Result comparisons - Internal or Benchmarks
06
Maturity Levels
-
Quick and easy assessment of practices
-
Prescriptive description of each level
-
Visualization on a maturity matrix
07
The 360° Evaluation
-
Individual assessment of selected employees
-
Evaluation by managers, colleagues and collaborators
-
Results per person and consolidated
08
Internal Survey
-
Employee survey
-
Control of participants while maintaining anonymity
-
Access to history and comparison of responses